Ratcheting Up Improvement Gains Through
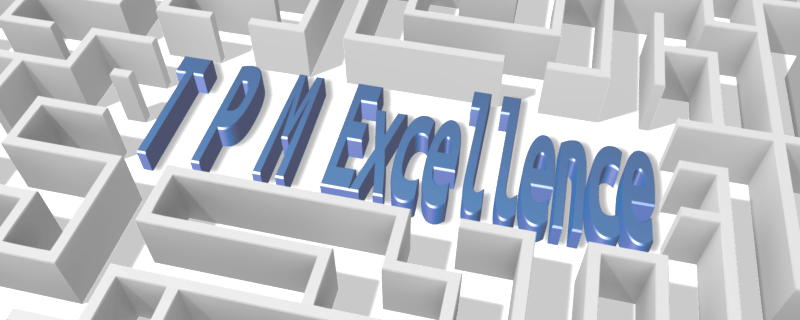
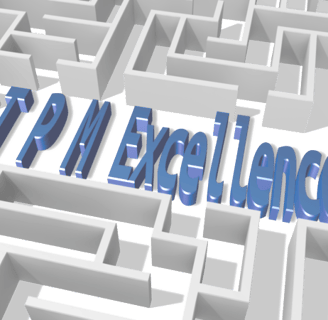
Programme Overview
The TPM Excellence programme establishes a practical improvement glide path as part of the daily routine. This team based process nurtures proactive mindsets and builds the collective capabilities essential for progress toward industry-leading performance.
The programme begins by with an assesmment of current operations and working sessions to align functional leadership priorities. This is followed by a practical, hands-on phase centred around asset improvement pilots. The goal is to drive measurable results through cross functonal team activities, embedding continuous improvement into daily routines and ultimately scaling lessons learned across the organisation.
The support programme develops internal capabilities to deliver rapid results and manage the future improvement glide path using practical projects to enhance:
Leadership Competence.
Execution Excellence.
Planning and Performance Analysis.
Laying the Foundation for Excellence
The programme starts by building a clear, evidence-based understanding of your current operations and creating alignment around a practical path forward. It involves:
Conducting a comprehensive diagnostic assessment to evaluate the current state of the systems that drive both performance and change. This includes:
Operational systems such as process control, data use, standardisation, and Leadership Standard Work
Improvement systems such as policy deployment, collaboration practices, and performance analysis
Facilitating “Plan the Plan” working sessions for leadership. These are designed to:
Develop a shared view of the full improvement landscape
Align on priorities that matter most to the business
Define and launch a pilot programme based on real-world, practical projects
Bring visibility to barriers and actively engage all levels in designing new ways of working
Partnering with internal teams to establish a structured rhythm of feedback and reflection. This ensures:
Timely capture of lessons learned
Continuous adjustment and alignment of activities
Scalable delivery of improvement gains across your wider operations
A Practical, Hands-On Approach
The programme mobilisation kicks off with a 3–4 day interactive workshop, blending theory with practical application. Participants:
Learn TPM principles and techniques and case studies.
Apply their knowledge in teams to real assets using the Asset Improvement Plan workbook—a structured, hands-on guide that drives understanding, root cause analysis, and countermeasure development.
Teams conclude the mobilisation workshop by capturing lessons learned and identifying improvement barriers. These insights feed into a “Plan the Plan” session that sets priorities and launches a pilot programme led by a cross-functional Core Team.
Bottom Up Delivery
Over a quarterly cycle, the Core Team meets 8–10 times to work through each stage of the Asset Improvement Plan:
Assess asset condition and performance
Identify problem hotspots
Measure improvement potential
Develop and implement countermeasures
Simultaneously:
Functional leaders use case studies from the mobilisation workshop to coach and align their teams.
Cross-functional alignment ensures improvement actions support business objectives.
Routine performance management processes embed the work into day-to-day operations.
Top Down Guidancce
In addition to improving asset performance, the improvement core team highlight gaps, barriers to progress and opportunities to resolve them by creating a sustainable “improvement glide path”.
That provides top down leadership with the vehicle to deliver:
Coaching for team leaders to develop front-line capabilities.
Increased engineering capacity by reducing unplanned downtime.
Stronger collaboration between production and maintenance teams.
That includes the development of policy standards to:
Extend component life by reducing wear.
Reduce human error, a major cause of downtime.
Improving data use and ownership of improvement.
Free up time to address precision and quality issues.
To scale these gains, we work with senior leaders to develop a bespoke Improvement Roadmap. That sets out a series of milestones setting out a staged journey to stability and higher-level performance. Each stage:
Builds capabilities
Reinforces consistent performance
Prepares your organisation for future challenges
Even mature operations benefit—systemic variation and unplanned events mean there’s always room to learn and improve. Leadership engagement is key, and this programme enables leaders to link local actions to strategic outcomes.
Delivering Business Goals
Programme delivery relies on practical, real-world projects led by team leaders who coach their teams to deliver business goals as part of the performance management framework. That creates:
1. A Quarterly Improvement Cadence linked to strategic execution to deliver:
Targeted performance analysis and problem solving
Smooth transitions in roles and responsibilities
Recognition of achievements to reinforce a culture of improvement
2. An Improvement Pull that links top down aspirations with bottom up delivery using:
Assigned operational hotspots to frontline teams.
Aligned problem ownership and continuous learning priorities.
Why This Matters Now
The TPM Excellence Programme is a proven pathway to stronger results—financially, operationally, and culturally. It enables your business to meet shifting expectations and navigate future disruption with confidence.
Let’s explore what this could look like in your organisation. Our support begins with:
A diagnostic to assess current systems and improvement readiness.
A collaborative planning session to align goals and launch a tailored pilot.
Ongoing coaching to embed learning, track progress, and scale success.
You’re not alone in this. Partner with us to unlock the full potential of your operations and build a high-performing, resilient future.
For senior manufacturing managers, that not only delivers operational enhancement, it enables a disciplined, inclusive, and data-driven approach that continuously elevates performance and secures long-term competitive advantage.
DAK Consulting
Chiltern House
45 Station Road
Henley on Thames
RG9 1AT, UK
Info@dakconsulting.co.uk
www.dakacademy.com
+44 (0)1491 845504